What is a Stepper Motor?
A stepper motor is a type of brushless DC electric motor that moves in precise angles, called steps, by converting a series of electrical pulses into rotational motion. They will not produce continuous motion from a continuous input voltage, and it will stay at a particular position as long as the power is “on”. Step motors are controlled with the use of discrete electrical pulse signals. Each pulse will rotate the step motor shaft by a fixed angle called a “step”. ISL Products can offer stepper motors with several different step angles (0.45°, 0.9°, 1.8°). ISL offers a concierge approach, ensuring that our Stepper Motors perform as intended within your application. You can learn more about our dedicated approach by reading a recent case study.
If the pulses are carried out in a specified sequence, the motor will spin continuously; the speed can be controlled by the rate at which the pulses are sent. These natural step angles allow a step motor to be accurately positioned without the accumulation of error. The step motor produces output torque from the interaction between the magnetic field in the rotor and in the stator. The magnetic field strength is proportional to the amount of current applied to the windings as well as the amount of turns in the windings.
Stepper motors fill a unique niche in the motor control world. A stepping motor can be used in a wide range of measurement and control applications throughout various industries. Sample applications include Ink Jet Printers, CNC machines, 3D Printers, Automation & Packaging machines, Security & Surveillance systems, Medical Tools & Equipment, Robotics and Vending machines. If you’re thinking about using a stepper motor in your next design, consult with our engineers today!
Stepper Motor Construction
A stepper motor consists of a permanent magnet sandwiched between the two rotor halves (causing axial polarity), which make up the spinning part of the motor, placed into a stator housing where the stator coils of wire make up the different motor phases. A bipolar stepper motor, also known as 2 phase hybrid stepper motors, each phase has four coils. The phase is magnetized where the A and A- phases (or B and B-)are magnetized at the same time so that both A phases are magnetized as one pole, and both A- phases are magnetized as the opposite pole because the winding direction of the A-phase is opposite the winding direction of the A- phase.
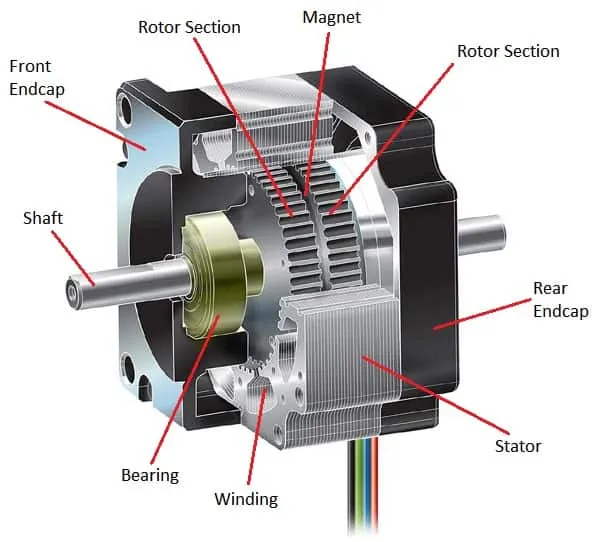
The rotor is connected to the motor shaft, which gives the output rotation and torque of the motor when voltage and current pulses are applied to the motor windings. The bearings on either side of the rotor allow for smooth rotation with little friction and wearing. The bearings are placed into their designated spaces in the front and rear end caps, which allow for the concentricity of the rotor inside the stator. Perfect alignment of the rotor and the stator is very important because the air gap between them, where the motor torque is generated, must be equal on all sides and is only a few nanometers wide – thinner than a strand of hair. If you’re having trouble narrowing down your exact stepping motor requirements, let us help.
Three Types of Stepper Motors
There are a few different types of stepping motors. Your application will dictate which type of motor will be optimal.
-
- Hybrid Stepper Motors – a motor that combines the power of PM and VR steppers! With a permanent magnet core and a toothed circumference made of plain iron, this motor offers unrivaled angular resolution and torque.
- Permanent Magnet Stepper Motor – with its rotor made of powerful permanent magnets, it skillfully interacts with the electromagnets of the stator, resulting in exceptional rotation and torque. This type boasts low power requirements and can generate high torque per unit of input power.
- Variable Reluctance Stepper Motor – a unique type of stepper motor. Unlike other motors, it doesn’t have permanent magnets. Instead, its rotor is made of plain iron and resembles a gear with teeth around its circumference. These teeth give the VR stepper a remarkable level of angular resolution. However, this precision often comes at the cost of torque. So, while VR steppers may not be the strongest, they are certainly a fascinating choice for those seeking accuracy in their motor applications.
Unique Features & Advantages of Stepper Motors
- Brushless – Stepper motors are brushless, which means they have a high reliability with little maintenance. The commutator and brushes of conventional motors are some of the most failure-prone components, and they create electrical arcs that are undesirable or dangerous in some environments.
- Load Independent – Stepper motors will turn at a set speed regardless of load as long as the load does not exceed the torque rating for the motor.
- Open Loop Operation – Stepper motors move in quantified increments or steps, providing exceptional positioning. As long as the motor runs within its torque specification, the position of the shaft is known at all times without the need for a feedback mechanism.
- Holding Torque – Stepper motors are able to hold the shaft stationary.
- Excellent response to start-up, stopping and reverse.
- Inherently more fail safe than servo motors.
ISL Products can offer a wide variety of stepping motors to fit all of your application needs. If your looking for a competitive quote, we can help with that too!