What is a Brushless Motor?
A Brushless or BLDC motor converts supplied electrical energy into mechanical energy using electromagnets in the stator to spin permanent magnets on the rotor, without the need for brushes. Brushless motors offer high efficiency and feature superb controllability.
How does a Brushless Motor Work?
As their name implies, BLDC motors do not utilize any internal brushes. To negate the need for brushes, brushless motors don’t have coils located on the rotor. Instead, permanent magnets are affixed to the rotor and the coils are relocated to the stator which is attached to the motor body. Since the coils are no longer spinning, there is no need for brushes. The motor commutation is electrical instead of mechanical, by alternating the magnetic poles of the stator windings to induce the rotation of the motor.
In a brushless DC motor, the permanent magnets on the rotor are spun by changing magnetic field directions generated by motor windings. Precise rotational control is accomplished by adjusting the magnitude and direction of the current flowing into these coils.
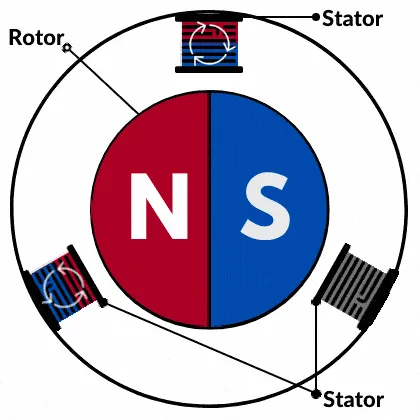
What are the advantages of a BLDC Motor?
A brushless DC motor is a unique motor type with slightly more advanced motor technology. First off they don’t have any components that experience relatively quick mechanical wear, so there is a lesser need for maintenance. The brushes inside of a brushed DC motor experience mechanical wear over time, from usage, and eventually render the motor useless. At that point, you have two options, either replace the brushes or use a new motor.
The lack of brushes also means that there is no dust or sparks, leading to less heat and noise generation. Electrical noise is the direct effect of strong sparking that takes place within a brushed motor as the brushes pass over the commutator. This key advantage leads to a very low electrical noise, which is why BLDC motors are preferred in applications where limiting electrical noise is important.
There are advantages to brushless DC motors beyond the lack of brushes. BLDC motors also deliver power more efficiently. When compared to a brushed motor, a brushless DC motor can output more continuous torque in a more compact size. A brushed DC motor would need much larger magnets to offer the same torque output, increasing the size and cost of the motor.
An electronic motor controller used to drive a brushless DC motor is more efficient at delivering power, which results in a higher rotational speed. The increased efficiency also allows these motors to run for longer periods of time at these high speeds. This ultimately allows for longer duty cycles and wider application suitability.
Types of BLDC Motors
Brushless direct current motors are available in two main layouts: Outrunners and Inrunners. Inrunners are similar to a normal brushed motor with a centered rotating shaft coming out of the motor. Outrunners, on the other hand, inhabit permanent magnets positioned around the outside that spin around the inner electromagnets. Essentially, an inside-out version of the inrunner.
Stepper motors are a type of inrunner brushless motor. It is unique in that it rotates in precise angles, referred to as steps.
Gearboxes can also be added to most types of BLDC motors, to provide increased torque outputs. Most commonly, planetary gearboxes are used to provide an efficient inline solution.
Unique Parameters
Oftentimes, brushless motor specifications will note unique parameters to describe their performance. To help you understand what these values and parameters mean, we have noted some of the more commonly used below.
Back EMF Constant (kv) is used to find the amount of no-load RPM per volt. If you see a 12VDC, 450 kv rating, this means the motor would run at approximately 5,400 RPM at no-load. (12V*450kv=5,400RPM)
In standard units, kv is expressed in Volts / (radians/second).
To be more precise, the kv rating is dependent on the back electromotive force (emf) constant of the motor. Similar to normal brushed motors, higher kv means higher RPM but lower torque and acceleration.
Torque Constant (kt) explains the motor’s torque output at a given current draw. Dimensional analysis can be done with the SI units of this constant which will make you realize it is the reciprocal of the kv rating. In short, kv = 1/kt and vice versa.
In standard units, kt is expressed in Newton Meters / Amp.
Conclusion
As Brushless motors become increasingly affordable they are replacing brushed motors to carry out the same tasks that brushed motors have performed for decades in some of the most common applications. With the increased deployment of brushless motors, more customers are requesting them for a range of applications across every industry. We have seen a significant increase in usage within industrial applications, automotive applications, medical applications, as well as power tools.
ISL Products has been designing and manufacturing brushed and brushless motors for decades, specializing in value-added solutions. By contacting one of our Applications Engineers you can save up to 10 hours during the motor selection process.