When selecting a dc motor for your application, one crucial decision you’ll face is whether to choose a brushed or brushless motor type of motor. This page will guide you through the key factors to consider when deciding between a brushless and brushed motor. From examining their construction and operation to evaluating their performance, we will discuss these two types of motor in detail. At the end, you’ll have a clear understanding of which motor is best suited for your specific application. Let’s look deeper into the brushless vs brushed motor debate to help you make an informed decision.
What are the differences between Brushless motors and Brushed motors?
Brushed Motor
A brushed motor, or brush motor, is a simple design that converts electrical energy into mechanical energy. It consists of several key components: a permanent magnet, a rotor, a stator, brushes, and a commutator.
The working principle is straightforward. When an electric current flows through the rotor’s armature windings, including rotor windings, it generates a magnetic field. This field interacts with the permanent magnet on the stator, causing the rotor to rotate. The brushes, typically made of carbon or precious metals, maintain constant physical and electrical contact with the commutator, which is a segmented metal ring that acts as an electrical switch to controls the electrical flow to the coil.
The rotating commutator plays a vital role in the motor’s operation. It reverses the direction of the current every time the rotor completes a half turn, ensuring a continuous rotation. The brushes provide a connection between the input power source and the rotating commutator, allowing the current to flow and energize the motor.
The brushed dc motor‘s simplicity allows for easy control of speed and torque through varying the current polarity. However, it also leads to certain limitations, primarily the limited lifespan due to brush wear, as well as sparking. These drawbacks have led to the development of more advanced motor technologies, like brushless motors, which offer improved efficiency and durability. However, brushed motors remain widely used in various applications, ranging from power tools to household appliances.
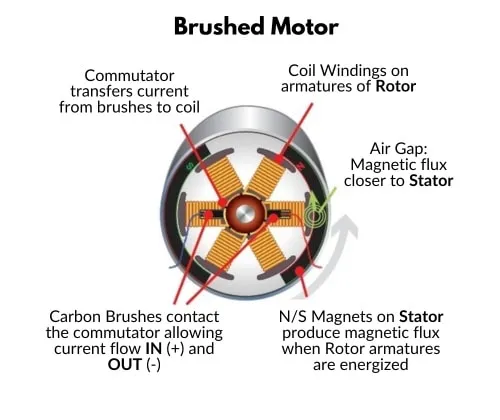
DC Motor & Small Gear Motor Basics
Brushless Motor
A brushless motor, or BLDC motor, is a type of electric motor that consists of a rotor and a motor shaft stator. Unlike brushed motors, it doesn’t have brushes and commutators. Instead, it uses electronic commutation to control the motor’s operation, providing enhanced performance metrics, including acceleration.
The working principle of a brushless motor is based on the electromagnetic interaction between the rotor and the stator. The stator contains multiple coils, which are strategically energized with electricity. As the current flows through these coils, it creates an electromagnetic field and a rotating magnetic field. The rotor, on the other hand, consists of permanent magnets. When the magnetic field of the stator windings interacts with the rotor’s magnets, it creates a rotational force.
To control the motor, hall sensors are used to detect the position of the rotor. This information is then sent to an Electronic Controller, which determines the timing and sequence of the current flowing through the stator coils. By precisely controlling the current, the motor can orchestrate the rotation of the rotor at desired speeds and in the desired direction.
The absence of brushes commutators prolongs the motor’s useful life and reduces friction, resulting in a more efficient and durable motor. These types of motors are found in a wide range of applications across various industries like robotics, electric vehicles, and industrial machinery.
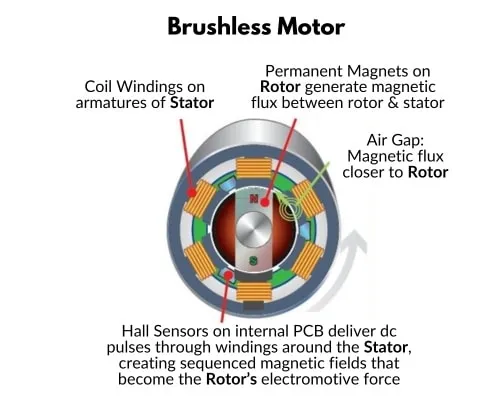
Key Components and How They Work
When discussing the key components of both brushed and brushless motors, it’s essential to recognize the differences that impact their functionality. Brushed motors use a commutator and brushes to maintain electrical contact, which can create electrical noise during operation and even torque ripple. In contrast, brushless motors utilize electronic controllers that reduce electrical noise by ensuring a smoother power supply to the motor. This electronic commutation eliminates the mechanical wear associated with brushes, resulting in less maintenance and longer service life. Understanding these components helps clarify why brushless motors are often preferred for applications requiring high efficiency and reliability.
Additionally, the power supply for both motor types plays a critical role in their performance. Brushed motors utilize a direct current (DC power supply), while brushless motors typically use electronic controllers to efficiently deliver power. This difference in power supply not only influences the overall efficiency of the motors but also their operational capabilities. By recognizing these key components and their respective functions, users can make more informed decisions when selecting the appropriate motor for their specific applications.
Key Components of BLDC and Brushed Motors
Brushed motors rely on physical contact through carbon brushes for commutation, whereas brushless motors utilize electronic controllers for commutation. The former has mechanical wear due to brush contact, leading to audible noise, limited speed range, and sparking. In contrast, the latter offers efficiency with none of the drawbacks, making them suitable for high-speed applications. Brushless motors exhibit longer service life and higher efficiency compared to brushed motors, making them ideal for various motion control applications.
Working Principle of BLDC and Brushed Motors
Both motors work around the same basic idea. Electricity is sent into a coil of wire which creates a magnetic field. This magnetic field interacts with stationary permanent magnets to create rotation.
In brushed motors, brushes and a commutator ring establish contact to move the electricity, creating friction leading to wear and electrical noise. Conversely, brushless motors replace brushes external electronic commutation, reducing mechanical noise and wear. Utilizing an electronic controller for commutation, brushless motors offer improved efficiency and lifespan. They generate less electrical noise due to the absence of physical commutators.
Key Components of BLDC and Brushless Motors
Brushless motors use permanent magnet dc motors and electronic controllers for operation, eliminating carbon brushes and electrical noise. In contrast, brushed motors rely on physical contact with brush assemblies for commutation, leading to mechanical wear and audible noise.
Brushless motors offer higher efficiency and longer service life due to their brushless design. They excel in motion control applications requiring precision and low maintenance. Deciding between brushless vs brushed motors depends on factors like cost, performance, and application requirements.
Working Principle of Brushless Motors
Brushless motors require electronic controllers for precise speed control. This controller energizes different coils of wire, known as poles, which interact with permanent magnets mounted to the rotor. These motors come in two styles; Inrunner and Outrunner.
Inrunner motors have a central rotor that is housed inside of the motor. The coils are mounted to the outside stator and act as a shell protecting the rotor.
Outrunner motors have a large outer rotor that houses the permanent magnets. The stator and its coils are on the inside.
Outrunners generate more torque and are more efficient, but lack the protection and cooling of an Inrunner.
Advantages and Disadvantages of Brushless and Brushed DC motors
Service Life
Brushed motors, with their physical brushes and replaceable brushes and commutators, are prone to mechanical wear and tear over time. The brushes gradually erode, limiting the motor’s lifespan. On the flip side, brushless motors – devoid of these physical contacts – boast a significantly longer service life. With fewer components susceptible to degradation, they endure extensive use with minimal deterioration.
Size
Size is an important factor when choosing a motor. Brushed motors tend to be bulkier due to the additional components like brushes and a commutator. In contrast, brushless motors exhibit a more compact design. Without the need for brushes, they are smaller and lighter while delivering comparable or even superior power. This size advantage makes brushless motors ideal for applications where space is at a premium.
However, brushless motors require an electronic controller or driver. This can be a small integrated controller attached to the motor, which will make the motor longer, or a much larger external controller that will need to be located somewhere else in the device. You will need to account for the additional electronics into the total size when integrating them into an application.
Speed and Acceleration
Brushless motors are known for their higher efficiency, leading to faster speeds and better acceleration compared to brushed motors. This is due to the precise control provided by electronic commutation in brushless motors, resulting in smoother and more consistent performance. On the other hand, brushed motors may exhibit lower speed capabilities and slower acceleration rates, making them more suitable for simpler applications that do not require high performance levels.
Speed Range
Brushed motors often operate at slower speeds in comparison to their brushless counterparts. The physical brushes can cause electrical limitations and increase the risk of sparking at higher speeds.
In contrast, brushless motors excel at a higher speed range. Their electronic commutation allows for precise control over speed. This enables smoother and more efficient operation across various speeds.
Efficiency
Efficiency is a critical differentiator between brushed and brushless motors. Brushed motors tend to be less efficient due to friction and wear on brushes, leading to energy losses.
Brushless motors, operating with electronic commutation, experience minimal friction and exhibit higher efficiency. They convert a larger percentage of electrical energy into mechanical energy, improving overall performance and reducing energy consumption.
Electrical and Acoustic Noise Considerations
One of the primary concerns when choosing between brushed and brushless motors is the impact of electrical noise and mechanical noise on performance. Brushed motors tend to generate significant electrical noise due to the arcing that occurs at the brushes and commutator. This electrical noise can interfere with sensitive circuits and lead to performance issues in applications that require precision.
Brushless motors, on the other hand, produce much less electrical noise since they do not rely on physical brushes. Their solid state commutation makes them ideal for environments where noise reduction is crucial.
In terms of acoustic mechanical noise, brushed motors can also be noisier due to the friction between brushes and the commutator, which can lead to vibrations and audible mechanical noise during operation.
Conversely, brushless motors, while often quieter, can still produce noise at high speeds due to air resistance and resonance. Since brushless motors have higher top speeds, this can be a serious consideration. Generally BLDC motors provide a quieter operation overall, making them suitable for applications like robotics and consumer electronics where noise levels need to be minimized.
Electrical Noise
Brushed motors use carbon brushes to achieve electrical contact for rotating the magnetic field, causing mechanical wear and noise. As the brushes make and break connections with the commutator ring arcing can cause noise, light, and sparks. These all create a load on the circuit. Adding capacitors to the motor terminals can help reduce electromagnetic interference or EMI. This is an affordable, easily implemented solution that works for most applications.
In contrast, brushless motors employ electronic controllers to interact with permanent rare earth magnets and create a rotating magnetic field without physical contact, reducing noise. Since digital controllers store and deliver electricity to the coils precisely, there is less electrical noise in the system. Electric controllers are generally more complicated to integrate into an application, but are ideal for sensitive applications like robotics, drones, and laboratory equipment.
Audible Noise Generation
Brushed motors can be noisy, primarily due to the physical contact between brushes and the mechanical commutator. As the brushes wear down, noise levels may increase. There are typically vent holes on the motors to provide cooling to the motor which can also amplify generated noise.
Brushless motors, operating with minimal friction, tend to generate less internal noise. However, since they can control the winding currents to rotate much faster, they tend to be loud due to air resistance and resonance. They can be quiet in applications like disk drives and medical dispensers where they’re operating in short bursts. They do tend to be louder in devices such as drones or electric vehicles where they’re operating at higher speeds for a consistent amount of time. Brushless drivers can also generate something called “Coil Whine”, a sound produced by electrical components when there is high current passing through them. In general we recommend the brushless motor for quiet operation.
Brushless DC Motor Controller
Utilizing a brushless DC motor controller can significantly enhance the performance and efficiency of brushless motors. These controllers regulate the speed and direction of the motor by precisely controlling the power delivery to the coils. By adjusting parameters such as voltage, current, and timing, a brushless DC motor controller can optimize the motor’s operation for specific applications, resulting in smoother and more reliable performance.
Additionally, brushless DC motor controllers offer advanced features like sensorless commutation, which eliminates the need for Hall-effect sensors by using back electromotive force (EMF) to determine the rotor position.
Choosing the Right DC Motor for Your Application
Finding the right motor for your project can be a daunting task if you do not know what aspects to consider. Here are some factors to consider when choosing between a brushed and brushless motor:
Cost
Cost is often a significant consideration when selecting a motor. Brushed DC electric motors are typically more affordable due to their simpler design and manufacturing process.
On the other hand, brushless motors tend to be more expensive. The additional cost for BLDC motors is the driver or controllers needed for operation. Depending on device life, you may be able to reach a motor lifespan that results in a cost savings over the long run. If your device is not going to outlast the lifetime of the motor, then a brushed motor is more cost effective.
The electronic controls involved with brushless motor implementation can also lead to more hours spent designing, troubleshooting and problem solving.
Consider your budget, manpower, and the overall cost-effectiveness of the motor based on your specific needs.
Performance vs. Size
If performance is your priority, brushless motors provide greater performance advantages. These motors provide a higher output power density, torque, and rotational speed capabilities compared to brushed motors. This makes them ideal for demanding applications, especially at very high speeds. Brushless motors also offer smoother and more precise speed control, ensuring better overall performance and efficiency.
Brushed motors offer a broader power range, and their simplicity makes them ideal for many applications. Reducing complexity can allow your whole application to perform better. If your design requires a broad torque range, a brushed motor is going to be the better option.
In general, brushless motors will provide more power and torque than similarly sized brushed motors. However, they will need a control module mounted somewhere on the application.
Balance the performance and size of the motor to the performance and size requirements of your application when deciding your next steps.
Gearbox Requirements
If you need additional torque, you will need to couple your DC motor with a gearbox. Either a fully integrated gear motor or external gearing will provide additional torque. The trade-off with any gearbox is that they also reduce the output speed and diminish efficiency.
For spur, worm, and planetary gearmotors it is necessary to remember that the input speed from the motor plays a critical part. If the input speed from the motor is too fast it will cause issues with internal gear engagement. Since brushed motors tend to operate at slower speeds, this is less of a concern. When coupling a BLDC motor with a gearbox, this is an important consideration.
Planetary vs. Spur Gear Motors
Control and Precision
Brushless motors provide better control and a high speed range, allowing for precise and variable speed adjustments. Since they need some sort of electronics to operate, they are more precise to start with. For the most optimal precision brushless motor, a Stepper Motor would be the choice.
Brushed DC motors can be very precise with additional electronics controlling them. Utilizing Pulse Width Modulation, or PWM, is an excellent way to control brushed motor speed and power consumption. Magnetic and optical encoders can be fixed to the motor to create Servo motors, which are great for precise positioning. Our DC Servo Motors are an excellent solution that utilize a brushed motor paired with an incremental encoder for precise, controlled movement.
By weighing these aspects against your project’s specific needs, you can make an informed decision that ensures optimal performance and cost-effectiveness between these two motor technologies.
At ISL Products, we provide top-quality brushed and brushless DC motors that offer market-leading performance. With over four decades of experience in the industry, we manufacture top-quality motors that meet the highest standards.
What sets us apart is our ability to customize our motors to fit your specific needs. Whether you require a unique size, voltage, or performance specifications, our team of experts is dedicated to delivering a solution that exceeds your expectations. We understand that every project is different and are committed to providing personalized solutions that address your specific requirements.
We have built a reputation for delivering products that consistently perform at the highest level, making us the trusted choice for customers worldwide. Contact us today to discuss your project requirements and let us provide you with the perfect motor solution.
Frequently Asked Questions (FAQs)
When considering the differences between brushed and brushless motors, it’s common to have questions about their performance and applications, including their disadvantages. One frequently asked question is whether brushed motors are better than brushless motors. While brushed motors can be more affordable and simpler to implement, they often have a shorter lifespan and require more maintenance due to brush wear. In contrast, brushless motors offer longer operation times and greater efficiency, making them suitable for demanding applications.
Another common inquiry is about the downsides of brushless motors. Although they excel in many areas, their initial cost can be higher due to the need for electronic controllers. Additionally, the complexity of their design may require more time for troubleshooting and maintenance. Understanding these nuances helps users make better decisions tailored to their specific needs.
What is the difference between a brushed and a brushless Motor?
The main difference lies in their construction and operation. Brushed motors use brushes and a commutator for electrical contact, while brushless motors rely on electronic commutation. This leads to differences in efficiency, noise levels, and maintenance needs.
Are brushed motors better than brushless?
Brushed motors have their advantages, particularly in cost and simplicity, making them suitable for certain applications. However, brushless motors generally outperform brushed motors in terms of lifespan, efficiency, and noise levels. The choice ultimately depends on the specific requirements of the application.
What are the downsides of a brushless motor?
The primary downsides of brushless motors include their higher initial cost and the need for electronic controllers, which can complicate integration and increase the overall expense of a project. Additionally, while they require less maintenance, troubleshooting can be more complex compared to brushed motors.
Do brushless motors last longer?
Yes, brushless motors tend to have a longer lifespan compared to brushed motors due to the absence of brushes and commutators, which are prone to wear. This durability makes them a preferred choice for applications requiring longevity and reliability.