In the manufacturing industry, motors complete the powerful task of converting electrical energy to mechanical energy. Stepper motors and Servo Motors both have distinct advantages and serve as common solutions for motion control projects. Determining the correct motor relies on specifications and application of use.
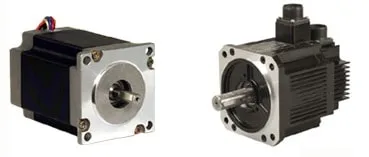
Torque & Speed
Both motors have different speed and torque characteristics, this can be the deciding factor on which motor is appropriate for the application at hand. At high speeds, stepper motors typically have poor torque characteristics. Servo motors can generate speeds anywhere between two and four times the speed of a stepper motor.
Servo motors operate under constant position feedback (closed-loop), as opposed to the typical open-loop system of a stepper motor. This allows servo motors to operate at higher speeds and generate higher peak torque. The use of rare-earth magnets in servos is an additional feature that enables them to create more torque in a small package.
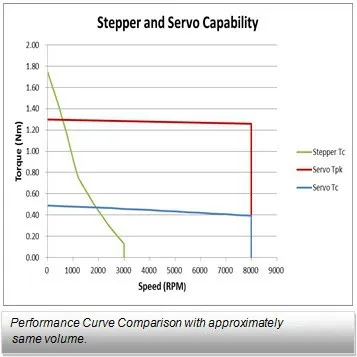
System Control
Usually, stepper motors operate in the open-loop, constant current mode. Stepper motor systems operating in a constant current mode (open loop) creates a significant amount of heat in both the motor and drive, which is a concern for some. Servo control solves this by only supplying the motor current required to move or hold the load.
Servo motors operate with a closed-loop system. Closed-loop control systems have encoders (sensors) to provide feedback. Feedback is data that is passed back from some point into the control system to another preceding point in the control system. Servos are controlled by sending an electrical pulse of variable width, known as pulse width modulation. When the system receives a pulse of some length it will then rotate the motor accordingly.
Pole Count
Stepper motors generally use 50 to 100 poles, whereas servo motors use only 4 to 12 poles. A pole refers to the area of a motor where a North or South Pole is generated by a permanent magnet or by passing current through coils of a winding. Each pole offers a natural stepping point for the motor shaft.
The high pole count of steppers allows them to generate holding torque, and consume less power at zero speed. Steppers don’t require encoders since they can accurately move between their many poles whereas servos, with fewer poles, require an encoder to keep track of their position.
Cost Analysis
Servo motors use rare-earth magnets and also have external features such as an encoder causing a higher cost. The physical size of a servo motor is larger than a stepper motor, requiring more raw materials to be manufactured.
Stepper motors are significantly less intricate. Stepper control systems are always less expensive and are optimal for applications that require low-to-medium acceleration, high holding torque, and the flexibility of open or closed-loop operation.
Servo motors are more costly due to the complexity of their internal design. Stepper motors use less expensive magnets and rarely incorporate gearboxes.
Which Motor Fits Your Application the Best?
Stepper motors are a good candidate for applications that require simple motion and no feedback. Steppers are available in a large variety of sizes, which helps to accommodate for size constraints.
Servo motors aid applications where sound and vibration need to be minimal. Servo motors are better for complex systems that require precise feedback. Certain applications such as CNC machinery require high accuracy, where a servo motor is an optimal solution. Servo motors are more efficient than stepper motors, with efficiencies between 80-90%.
In overall performance, servo motors are best for high speed, high torque applications while stepper motors are better suited for lower acceleration, high holding torque applications. ISL Products can help tailor the correct motor for all applications, small or large.
The table below will help you determine stepper motor vs servo for your next application requirements.
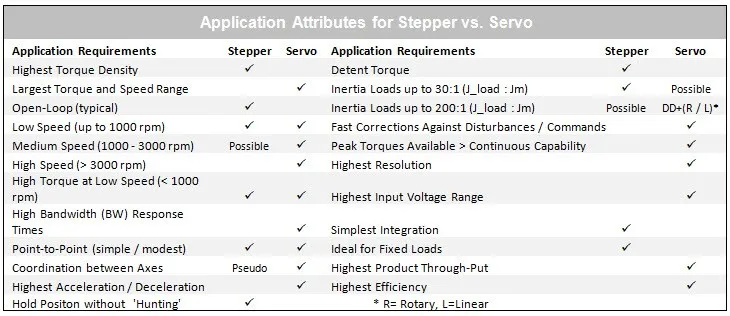