What is DC Servo Motor
Key Highlights
Precise Control: dc servo motors excel at accurate position, speed, and acceleration control.
- Versatile Applications: Used in robotics, automation, aerospace, and more.
- Feedback Dependent: Utilize feedback mechanisms (e.g., encoders) for precise operation.
- DC Powered: Operate on direct current, suitable for various power sources.
- Various Types: Available in brushed, brushless, and linear configurations.
- Customizable Options: Can be tailored to specific application needs.
What is a DC Servo Motor?
DC servo motors are very important in many industries today as we rely more on automation. They are different from regular dc motors. Servo motors focus on precise control. They use a feedback mechanism to reach and hold specific positions accurately. This article will look into how DC servo motors work, the different types, their uses, and why feedback is crucial for their function.
Understanding DC Servo Motors
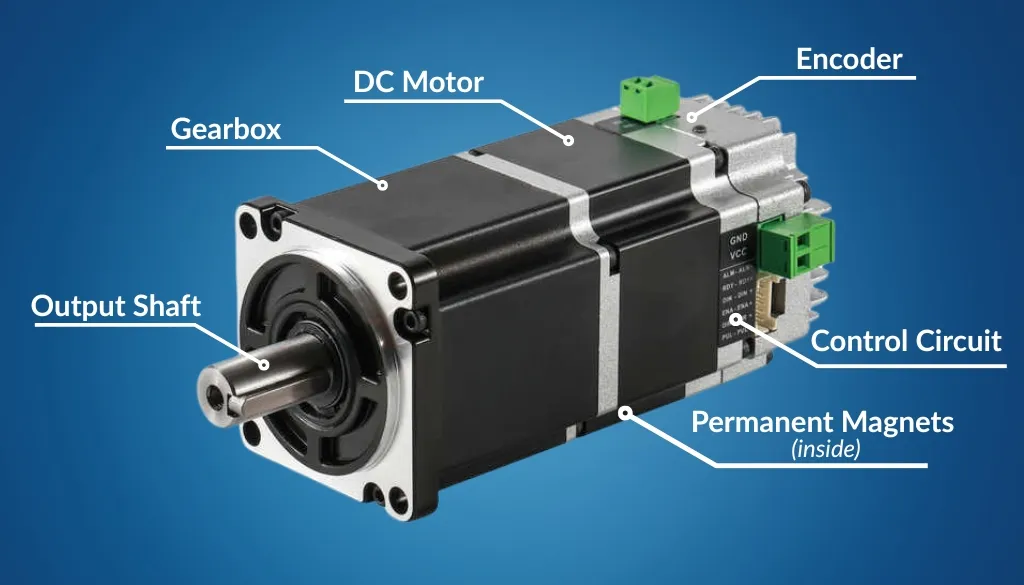
DC servo motors are a special type of motor. They are known for their ability to give precise control in many applications. They do this with a closed-loop monitoring system. This system always checks the motor’s position and changes the motor’s output to match what is needed. This closed-loop control sets servo motors apart from regular DC motors. Without an encoder, standard DC motors work on an open-loop system, which does not have position feedback.
Defining the DC Servo Motor
A DC servo motor uses direct current to turn it’s output shaft to a certain position. It can keep this position steady, even when outside forces act on it. Unlike regular DC motors that focus on on continuous rotation in direction, DC servo motors are great for precise and repeatable movements. These types of motors’ accuracy comes from a feedback system, usually an encoder. This system checks the position of the motor shaft and sends it back to the control circuit.
Key Components and Their Functions
A DC servo motor has many important parts that work together for it to function accurately:
- DC Motor: This is the main part, providing the power to rotate.
- Gearbox: This is used to increase the torque output and reduce the speed output of the motor depending on use case.
- Output Shaft: This is the part that spins and sends the power to wherever it is needed.
- Control Circuit: This handles input signals and manages how the motor works.
- Feedback Device (like an Encoder): This checks the position of the output shaft and gives updates to the control circuit.
- Permanent Magnet: This makes a steady magnetic field that works with the motor’s internal electromagnets to create movement.
The control circuit gets input signals, usually in digital form, that shows where the motor should go. It then utilizes the electrical signals and encoder feedback to produce precise movements.This ongoing feedback loop helps the motor get to and stay at the correct position.
The Mechanics of DC Servo Motors
The way a DC servo motor works depends on how its electrical and mechanical parts work together to convert electrical energy into mechanical energy. The control system gets input signals that show the desired position and tells the motor to rotate. But the real secret to a servo motor’s accuracy is its feedback system.
How Does a Servo Motor Work?
The control system sends electrical signals, sometimes a Pulse Width Modulation (PWM) signal, to the motor. This starts the motor to turn in the direction we want. At the same time, the feedback mechanism, such as an encoder, checks the motor speed and the position of the shaft. It sends this information back to the control system. Then, the control system compares the actual position to the desired position. If there is a difference, it creates an error signal. This signal helps adjust the motor’s power until the error is less and the desired position is reached.
The Role of Feedback in Servo Control
Feedback is very important for the precision of a DC servo motor. The feedback signal is always compared to the desired position, or setpoint. This helps the system adjust itself. The control circuit figures out the difference between the feedback signal from the position sensor, which shows the current position of the motor, and the setpoint. This difference creates an error signal. The error signal assists by allowing the control circuit to change how much power goes to the motor. This way, the motor can move precisely and hold its position. Without this feedback, it would not be possible to position accurately.
How does a DC servo motor work and what are its main components?
A DC servo motor works by receiving a control signal that determines the motor’s position. It consists of a motor, a feedback sensor (encoder), a controller, and a power supply. The controller compares the desired position with the actual position feedback from the encoder to adjust motor movement accurately.
Types of DC Servo Motors
DC Servo motors have many types to fit different needs. Knowing the types of servo motors is important when choosing a motor for a specific job.
Brushed vs. Brushless DC Servo Motors
Brushed DC Servo Motors: These motors are affordable and perform well. However, they have brushes and commutators that can wear out and need maintenance. The friction from these brushes can create electrical noise, which might be a problem in delicate electronic settings.
Brushless DC Servo Motors: Brushless DC motors are more efficient and last longer than brushed motors. They also tend to be quieter. Since they do not have brushes, and there is no friction or wear, BLDC motors have longer service lives. Brushless motors also produce less electrical noise, making them better for quiet environments. BLDC Motors do require external commutation, which can increase cost and complexity.
Gearbox Variations: Spur, Worm, and Planetary
- Spur Gearboxes: These gearboxes are simple and affordable. In a spur gearbox two or more gears are connected one after another, often using parallel shafts. This construction is less complex and easy to implement, but the full force of the motor and load are put onto each gear. They are best for jobs that don’t need high precision. But they may be less efficient and noisier than other types.
- Worm Gearboxes: These gearboxes are great for achieving high gear ratios in a small size. They utilize one large standard gear as well as strong spiral gear to create a very high reduction ratio. Because of the mesh between the gears, most worm gear motors have a right angle output shaft. They also have self-locking features, which is helpful when you need to hold a position against a load.
- Planetary Gearboxes: These gearboxes are known for high efficiency and a good torque-to-weight ratio. They utilize a central “sun” gear, and outside “orbital” gear, and several planetary gears in between. Since the planetary gears work together, the full load of the motor is split across 3 or more contact points. This allows planetary motors to handle higher torque loads with smaller footprints. They also offer precise motion control, however they usually cost more than other options.
Applications of DC Servo Motors
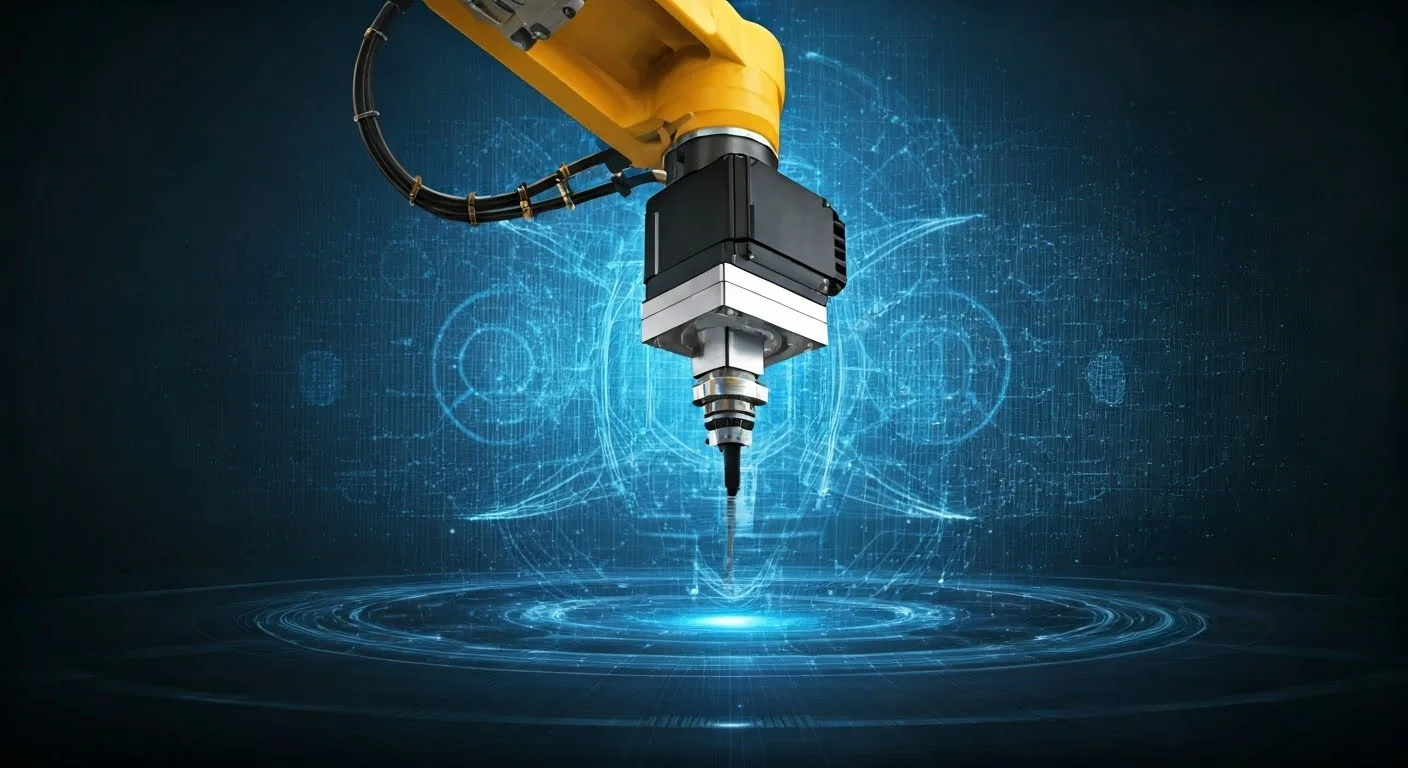
DC servo motors are very important in many areas because they can control position, speed, and acceleration well. Here are some key sectors where they are very useful.
Industrial Use Cases for Precision and Control
Industrial applications need precision and reliable performance, and they often use DC servo motors in various machine tools. These motors are key in many automation systems. They help achieve accurate control in tough environments. For instance, in CNC machinery, precise movements are very important for cutting, milling, and shaping materials.
Robotics
In robots, servo motors allow for accurate movements in arms, grippers, and walking systems. You can find them in robots that work in manufacturing, healthcare, and exploration. They provide precise control for robotic arms, allowing them to do complex work like assembly, welding, and handling materials with great repeatability.Their versatility means they end up in almost every application.
Consumer Electronics
DC servo motors are important not just for factories but also for gadgets and robots. They help devices like cameras move exactly right, which helps with focusing and stabilizing images. This incredible precision in a small footprint has helped with the increased miniaturization of everyday devices.
Another place where servo motors are likely to appear are dispensers. Automatic pet feeders, medication dispensers, and even robotic soap dispensers all utilize compact servo motors to provide a precise amount of items each time.
Design and Customization of DC Servo Motors
Standard DC servo motors are useful for many different applications. However, some cases need special changes to improve how they work or to fit certain needs. This section looks at how we can adjust servo motors to meet these different demands.
Tailoring Motors to Application Needs
Not all applications are the same. Different things like torque, speed, size, and work setting change a lot. Custom solutions for DC servo motors include changing parts of the motor to fit specific needs. This may require changing motor winds or gearbox to get the right torque and speed or using special materials to make it stronger in tough conditions.
Working with Engineers for Custom Solutions
Designing a custom DC servo motor usually requires working with skilled engineers. These experts help during the design process. They think about important details like load needs, speed settings, environmental conditions, and feedback systems that specific applications need for the best performance. This customized design makes sure that the motor fits well into the system and runs efficiently and reliably.
Comparative Analysis of DC Servo Motors
DC Servo Motors and AC Servo Motors cater to different application needs, each presenting unique strengths. While DC servo motors, using DC power, are known for their high output power capabilities, they excel in low-voltage applications that make them suitable for consumer electronics and robotics. They also work well with battery powered applications.
On the other hand, AC servo motors are preferred in environments requiring high-speed performance and smooth operation. They integrate better into large scale industrial applications. Their utilization of AC power tends to make them better for stationary applications.
Understanding these distinctions helps engineers select the right motor for their specific requirements, ensuring optimal performance and efficiency in their applications.
When comparing these two types, it is essential to consider their operational characteristics, including the key differences that define their performance. DC servo motors typically provide a higher starting torque, making them ideal for applications where immediate power is paramount. Conversely, AC servo motors maintain a consistent torque across a broader speed range. This comparative analysis of DC and AC servo motors illustrates the importance of selecting the right type based on power needs and operational demands.
AC Servo Motor vs. DC Servo Motor: Understanding the Differences
When distinguishing between AC and DC servo motors, several key differences emerge. AC servo motors are powered by alternating current and are primarily used in high-voltage applications, while DC servo motors operate on direct current, making them suitable for battery powered and low-voltage environments.
The control mechanisms also vary; AC servo motors typically utilize optical or magnetic encoders for position feedback, whereas DC servo motors sometimes use potentiometers instead. Furthermore, AC servo motors can deliver consistent torque at variable speeds, whereas DC servo motors provide high starting torque but will experience reduced torque at higher speeds. Understanding these key differences can guide you in choosing the appropriate motor for your specific application.
Pros and Cons: Balancing the Benefits and Limitations
When evaluating DC servo motors, it is vital to consider both their advantages and disadvantages.
Pros:
- High torque capacity suitable for various applications.
- Quick response times and efficient operation.
- Excellent for precise control of speed and position.
Cons:
- Maintenance requirements, particularly for brushed models.
- Potential for electrical noise due to brushes.
- Limited operational lifespan compared to brushless alternatives.
Weighing these pros and cons allows for informed decisions when selecting the appropriate servo motor for your specific project needs.
Conclusion
Understanding DC servo motors is important for many uses in both industry and everyday products, including applications with an industrial load. Their precise control and feedback systems help achieve accuracy and efficiency in movement. Whether you choose a brushed or brushless motor, or need specific gear types like spur, worm, or planetary, DC servo motors can be adapted to fit your project. Use the strength and reliability of DC servo motors in your next project. If you need help choosing the right motor or designing a special solution, please contact us.
Frequently Asked Questions
What Makes a DC Servo Motor Different from Other Motor Types?
A DC servo motor is different from a standard DC motor, a synchronous motor, or a stepper motor. It is made for precise position control. This motor uses a feedback mechanism. This helps it get and stay at exact positions. It is perfect for tasks where accuracy is very important.
Can DC Servo Motors Be Used in Outdoor Applications?
Yes, but there are some things to think about. Many DC servo motors work well indoors, but some are made for outdoor use. These outdoor models usually have special features. They often include sealed casings and materials that resist corrosion. This helps them last longer and work better in tough outdoor conditions.
How Do I Choose the Right DC Servo Motor for My Project?
Think about what your project needs. You should consider things like the torque you need, the speed of the motor, how precise you want things to be, the type of movement you need (whether rotary or linear), and the power supply. These factors will help you choose the right motor. You can also talk to an expert or look at the manufacturer’s datasheets for more guidance.
What Are the Maintenance Requirements for DC Servo Motors?
Maintenance needs are different depending on the type of servo motor. Brushed DC servo motors need more maintenance often because their brushes wear out. In contrast, brushless servo motors need less maintenance. This is because they do not have physical brushes. Usually, checking for wear regularly, keeping things lubricated (when needed), and ensuring a clean working area can help your DC servo motor last longer.
How Does Gearbox Type Affect a DC Servo Motor’s Performance?
The type of gearbox you choose can greatly affect how a DC servo motor works. There are several types of gearboxes, like spur, worm, and planetary. Each type has different strengths in torque output, speed reduction, and precision. For example, if you need high precision, a planetary gearbox is a good choice because it is very efficient and has little backlash. On the other hand, a worm gearbox is a better fit when you need high torque and self-locking features.